Porosity in Welding: Identifying Common Issues and Implementing Finest Practices for Prevention
Porosity in welding is a prevalent issue that typically goes unnoticed up until it causes substantial problems with the stability of welds. In this discussion, we will certainly check out the essential factors contributing to porosity development, examine its detrimental results on weld efficiency, and discuss the ideal methods that can be taken on to minimize porosity occurrence in welding procedures.
Common Sources Of Porosity
Utilizing filthy or damp filler materials can introduce impurities right into the weld, adding to porosity problems. To reduce these common causes of porosity, detailed cleaning of base metals, proper shielding gas selection, and adherence to ideal welding specifications are essential practices in accomplishing top notch, porosity-free welds.
Influence of Porosity on Weld Top Quality

The visibility of porosity in welding can substantially jeopardize the structural integrity and mechanical residential or commercial properties of bonded joints. Porosity develops gaps within the weld steel, deteriorating its overall toughness and load-bearing capability. These voids serve as stress and anxiety concentration points, making the weld a lot more prone to cracking and failure under used tons. In addition, porosity can reduce the weld's resistance to deterioration and other ecological elements, further diminishing its long life and performance.
Welds with high porosity levels tend to display reduced impact strength and decreased ability to flaw plastically before fracturing. Porosity can restrain the weld's capability to effectively send forces, leading to early weld failing and possible safety threats in vital frameworks.
Best Practices for Porosity Avoidance
To boost the architectural stability and top quality of welded joints, what specific actions can be executed to decrease the event of porosity during the welding procedure? Utilizing the right welding method for the particular product being bonded, such as adjusting the welding angle and gun placement, can further stop porosity. Routine assessment of welds and instant removal of any type of concerns identified throughout the welding procedure are vital methods to stop porosity and generate top quality welds.
Value of Appropriate Welding Techniques
Carrying out proper welding techniques is extremely important in making sure the structural dig this honesty and high quality of bonded joints, building upon the structure of effective porosity avoidance procedures. Excessive warmth can lead to enhanced porosity due to the entrapment of gases in the weld swimming pool. In addition, utilizing the proper welding criteria, such as voltage, current, and take a trip speed, is critical for accomplishing audio welds with minimal porosity.
In addition, the choice of welding process, whether it be MIG, TIG, or stick welding, should align with the certain requirements of the task to guarantee ideal outcomes. Proper cleaning and prep work of blog here the base steel, in addition to selecting the best filler product, are also necessary parts of competent welding techniques. By adhering to these ideal techniques, browse this site welders can lessen the danger of porosity formation and generate high-quality, structurally sound welds.
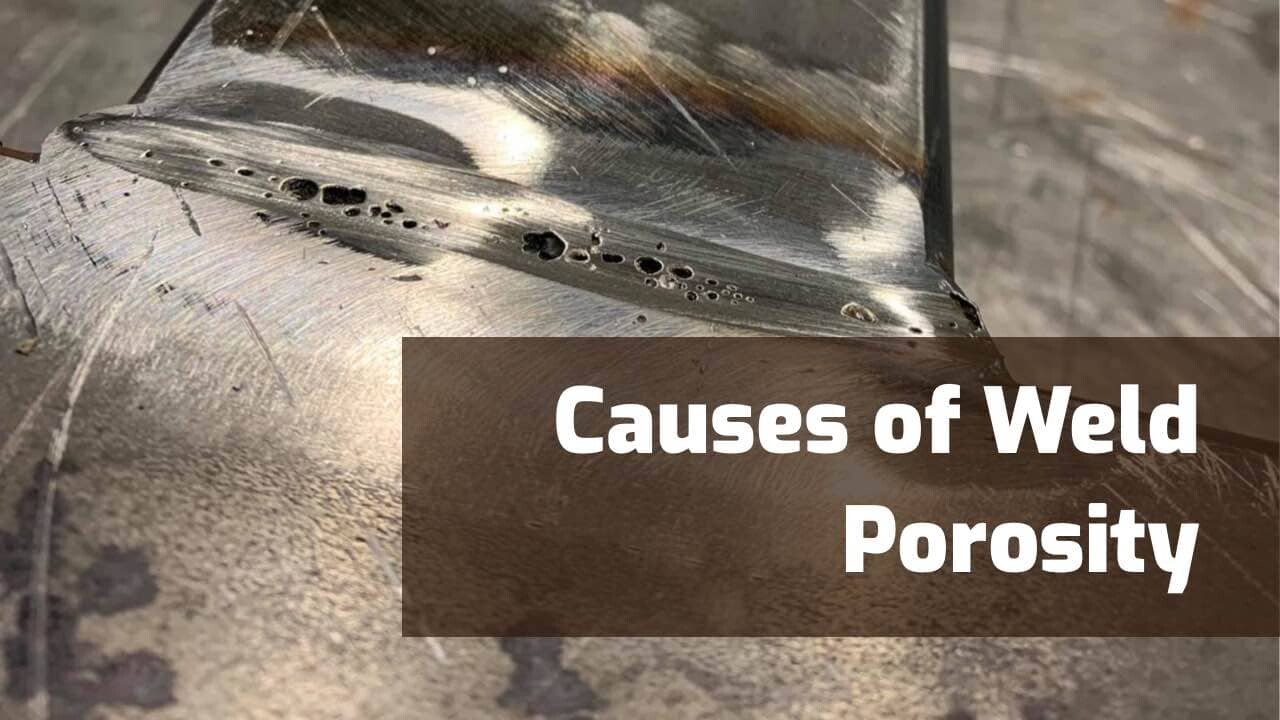
Evaluating and Quality Assurance Actions
Quality control measures play a critical function in verifying the integrity and dependability of welded joints. Examining procedures are vital to find and protect against porosity in welding, guaranteeing the strength and resilience of the end product. Non-destructive screening approaches such as ultrasonic testing, radiographic screening, and aesthetic assessment are generally used to identify potential defects like porosity. These strategies enable the assessment of weld top quality without endangering the stability of the joint. What is Porosity.
Post-weld examinations, on the other hand, analyze the final weld for any problems, including porosity, and verify that it meets defined requirements. Applying a thorough quality control strategy that consists of comprehensive testing treatments and inspections is critical to decreasing porosity problems and making certain the total top quality of welded joints.
Verdict
To conclude, porosity in welding can be an usual issue that affects the high quality of welds. By recognizing the typical reasons for porosity and implementing ideal techniques for avoidance, such as correct welding strategies and screening measures, welders can ensure top quality and trusted welds. It is important to prioritize avoidance techniques to lessen the incident of porosity and keep the integrity of welded structures.